Sustainability at Walker's
As a family-run business for over 125 years, Walker’s has always maintained its faithful commitment to its homegrown roots in the stunning Speyside region of the Scottish Highlands, ensuring a conscious concern for the food we produce, the welfare of the local workforce, working environment and its important relationships with local suppliers and businesses.
Being one of the largest employers in a small area, the Walker family has developed a social responsibility and mutual inter-dependency with the local community. People are at the heart of our business and it has always been natural for Walker’s to operate in a caring fashion by looking after our workforce. Many contemporary attitudes to business are practices that Walker’s have been carrying out for over 100 years.
Walker’s are continually striving to develop strong social and environmental policies that ensure the Company continues to meet the many international standards for product safety whilst simultaneously protecting the environment and their workforce.
Business Specific Achievements
- Walker’s Shortbread is baked with no genetically modified ingredients, artificial colors, flavors, preservatives or hydrogenated fats.
- The Company is a member of the Roundtable on Sustainable Palm Oil, for sourcing palm oil from sustainable forests. All of the Palm Oil Walker’s use is certified sustainable.
- No bovine growth hormones are given to the free range grass fed dairy cows that produce the rich, creamy milk that becomes the butter used in our shortbread recipe.
- 100% vegetarian; no animal fats are used in any of Walker’s recipes. The Company is also a member of the Vegetarian Society.
- Raw ingredients sourced as locally as possible.
- Support local trades, businesses and charities.
- Committed to the Ethical Trading Initiative.
- No hardened vegetable oils are used in our chocolate. Chocolate is Cocoa Horizons certified.
Factories
Walker’s Shortbread operates four factories in Aberlour and two in nearby Elgin.
An energy efficient, induction lighting program has been implemented and we are now in the phase of an LED replacement program. Since implementing the LED lighting and replacement program we have replaced over 1,300 lighting units. The LED and induction lighting uses 50% less energy than conventional lighting. LED lighting also reduces the number of lighting units required by nearly 40%, resulting in a much lower energy and resource requirement to meet our lighting needs, while maintaining the high visibility levels required for continual visual quality checks.
Energy efficient condensing boilers have been installed in all four factories at the Aberlour site giving a 40% energy efficiency saving compared to traditional boilers. At our Elgin site 6 old boilers were upgraded with energy efficient boilers. At our Aberlour site 2 old large boilers were upgraded with smaller more energy efficient boilers.
The original village bakery in Aberlour has been adapted as a test bakery for new product development in support of the business.
Solar Panels
As part of the Company’s on-going commitment to environmental improvement Walker’s have recently installed 80 solar panels on the roof of the newest factory. They are currently producing clean, green renewable energy for the site.
It is a 20 kW system and is on target to produce an average of 12,000 kWh (units) of electricity per annum. The panels will continue to produce electricity and have a life expectancy of 25 years or more.
This system of PV (photovoltaic) panels avoids approximately 8 tonnes of CO2 from being released into the atmosphere each year.
Packaging
- The gauges for film, cardboard, tin plate and plastic have all been reduced where permissible and practicable.
- Extensive work carried out on reductions to both primary and secondary packaging.
- The cardboard for selected cartons is sourced through the Forest Stewardship Council to ensure sustainability.
- Use of recycled tinplate.
- Plastic (rPET) – includes a recycled content in excess of 50% and can be recycled.
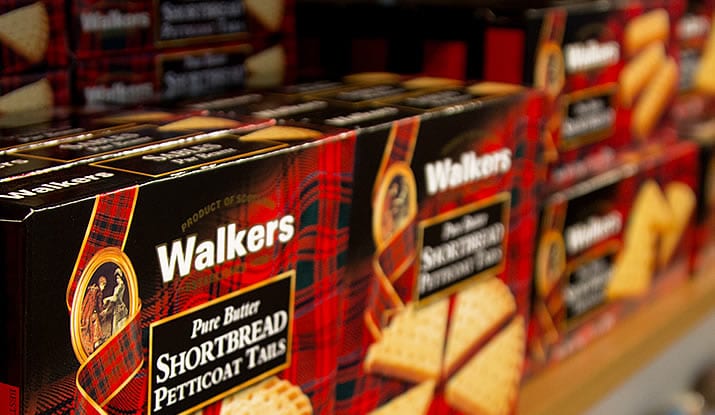
Energy
- Members of the government controlled CCA (Climate Change Agreement) since inception in 1998. We have reduced our carbon emissions (CO2e per tonne of production) by over 13% since the baseline year.
- Audited by the Carbon Trust.
- Electricity use monitored every half hour to identify areas for improved efficiency.
- Building management systems installed in our two newest factories.
- Changed oven fuel from oil to gas reducing carbon emissions.
- Reduced wasted ‘heat up’ and ‘cool down’ times to achieve optimum oven temperatures only when needed for baking.
- Specialist oven survey has been carried out to save energy, whilst ensuring optimal performance.
- Where possible energy efficient control systems are fitted to existing / new machinery, for example motor inverters and soft starts for fans.
- All air compressors are fitted with new variable speed drives.
- Heat recovery system has been integrated into the compressed air system, in one of the factories.
- Replacing old inefficient centralized boilers for smaller energy efficient on demand boilers.
Water
- We understand the need to value water as a precious resource and manage it throughout all our Company operations to ensure that it is not wasted.
- We have a water use monitoring program.
- Water use is monitored weekly against production figures and readings are recorded weekly.
- Fitted timers, auto taps and spray nozzles to hand-wash stations in processing areas.
- Toilet-flush reduction program implemented.
- Full compliance with government controlled waste water regulations.
- Changing water arrangements has minimized as far as practically possible the volumes of water used per annum, while maintaining necessary hygiene standards.